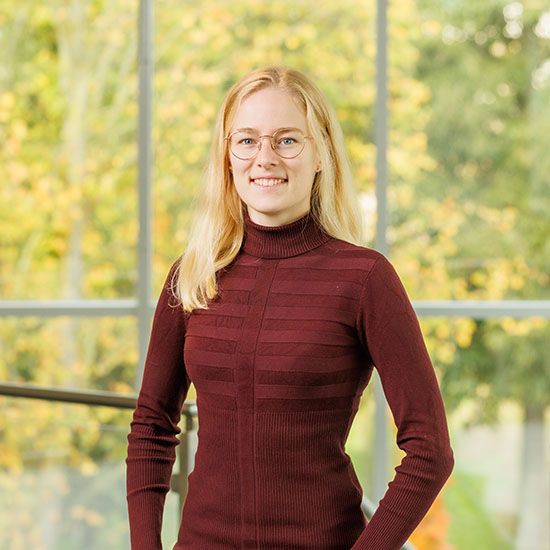
creating consistent dimensions.
The CFD simulation is performed in 2D, to keep simulation times low. A porous domain with a high resistance is added to the end of the domain to simulate the resistance caused by the extrusion head of the machine. One of the main challenges of the CFD simulation was the mesh. Normally a stationary and rotating mesh combination is used for rotating geometries, but this approach is not possible as the two gears mesh together. Remeshing the geometry for each timestep proved to be very time consuming in both mesh time and simulation time. Additionally the quality of the mesh was not good enough to resolve the high gradients of pressure and velocity between the teeth. To solve this, the meshing software TwinMesh was used.
Using TwinMesh we were able to create a structured mesh for each gear, that is ‘compressed’ between the teeth. The structure and element numbering is kept exactly the same between timesteps, only the rotation and compression is changed. The results of the CFD simulation are shown on the right and predicts the pulsation caused by the external gear pump.
The experimental set-up is similar to the machine from the CFD simulation and was used to validate the simulation results. More information can be found in the elaborate PDF below.

"visualizing flow"
Understanding the internal dynamics of a system can be a complex task, especially when only the output, such as the extruded rubber strip and a pressure sensor in this case, is available. However, the use of computational fluid dynamics (CFD) simulations proved to be invaluable in tackling this challenge. The CFD simulations of the pump provided a clear visualization of the internal fluid dynamics of the rubber, allowing for a deeper understanding of the pulsation behavior. Furthermore, the simulations facilitated the testing of a novel approach to modify the pulsation behavior, which would have been expensive to achieve through experimental testing alone. Remarkably, the simulation results were in excellent agreement with the experimental data obtained subsequently, underscoring the effectiveness of CFD simulations in addressing engineering challenges. This showcases the power of utilizing CFD simulations as a valuable tool in gaining insights and optimizing system performance in complex situations.
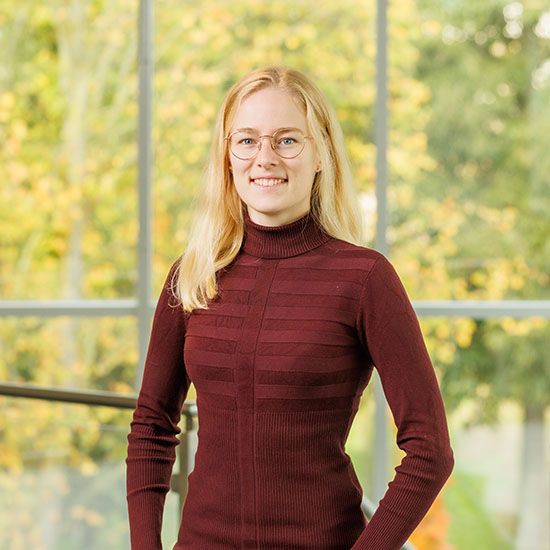
explore more cases.
Demcon multiphysics.
Demcon multiphysics is an engineering agency with high-end expertise in the area of heat transfer, fluid dynamics, structural mechanics, acoustics, electromagnetism and nuclear physics. We support clients from a wide variety of market sectors and help them achieve their goals in research and development with deep physical insights.
We combine fundamental physical knowledge from an analytical approach with Computer Aided Engineering (CAE) simulations tools from ANSYS, MATHWORKS, COMSOL, STAR-CCM+ and FLUKA to setup, execute, analyze and evaluate numerical simulations. The use of Computational Fluid Dynamics (CFD), Finite Element Analysis (FEM / FEA), Lumped Element Modelling (LEM), Computational Electromagnetics (CEM) and Monte Carlo simulations enables us to make a virtual prototype of your design. With these techniques we can simulate the fluid and gas flows, energy exchange, heat and mass transfer, stresses, strains and vibrations in structures and the interaction of electromagnetic fields with other physical aspects like heat generation. Simulation-driven product development increases the development efficiency and reduces the product development time. Our services can therefore fully support you in the designing phase, from idea up to prototype, from prototype to final design.
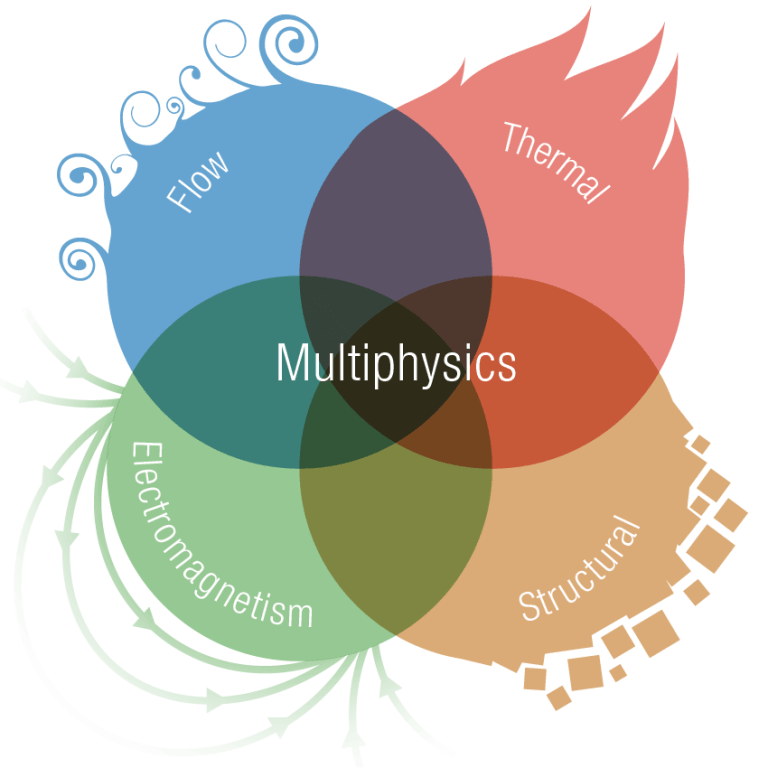