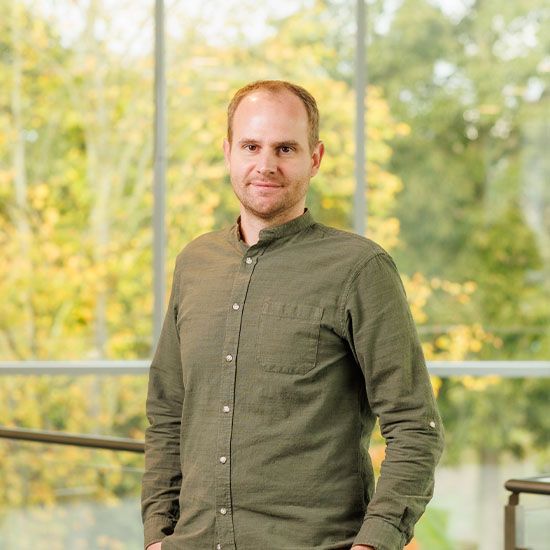
Web handling involves the processing of thin materials through a processing setup using industrial machinery. Common types of web handling processes include coating, laminating, and metallizing for the creation of layered thin foil structures. These structures act as semi-finished products. Performance of such products can be improved by making the foils extremely thin in the order of tens of microns. However, such thin foils are hard to handle, in a continuous process. Enhanced web handling will help to make better products and contribute to accelerate the transition toward renewable energies, i.e. more powerful, thinner, lighter and more flexible products.
During their production, layers are deposited at high temperatures on a substrate material to create thin foil structures. However, as the foils get thinner and wider, especially web handling becomes an issue. Thin foils can start to crack as the handling forces are relatively large compared to the low strength at high temperatures. Moreover, the foils are getting extremely flexible at high temperatures possibly causing the foil to buckle or wrinkle. The question is then which handling forces and which temperature gradients result in a robust production process. We have helped several clients with these kind of engineering questions to generate a robust production process.
improving web handeling.
The process of web handling at high temperatures can be modeled employing simulation software. First, temperature profiles of the foils can be determined by including thermal contributions such as heaters, insulators, and heat distributors. Second, the deformations (such as buckling and wrinkling) can be determined which are caused by thermal expansions and web handling forces such as web tension controllers, roller interaction, spraying processes or air nozzles.
In this way existing processes can be investigated and critical process parameters can be determined from sensitivity analyses. Moreover, new designs can be realized from scratch, for example based on web rollers, a flotation oven or a vertical oven concept. Concept choices can be made based on fundamental insight and the processes can be optimized.
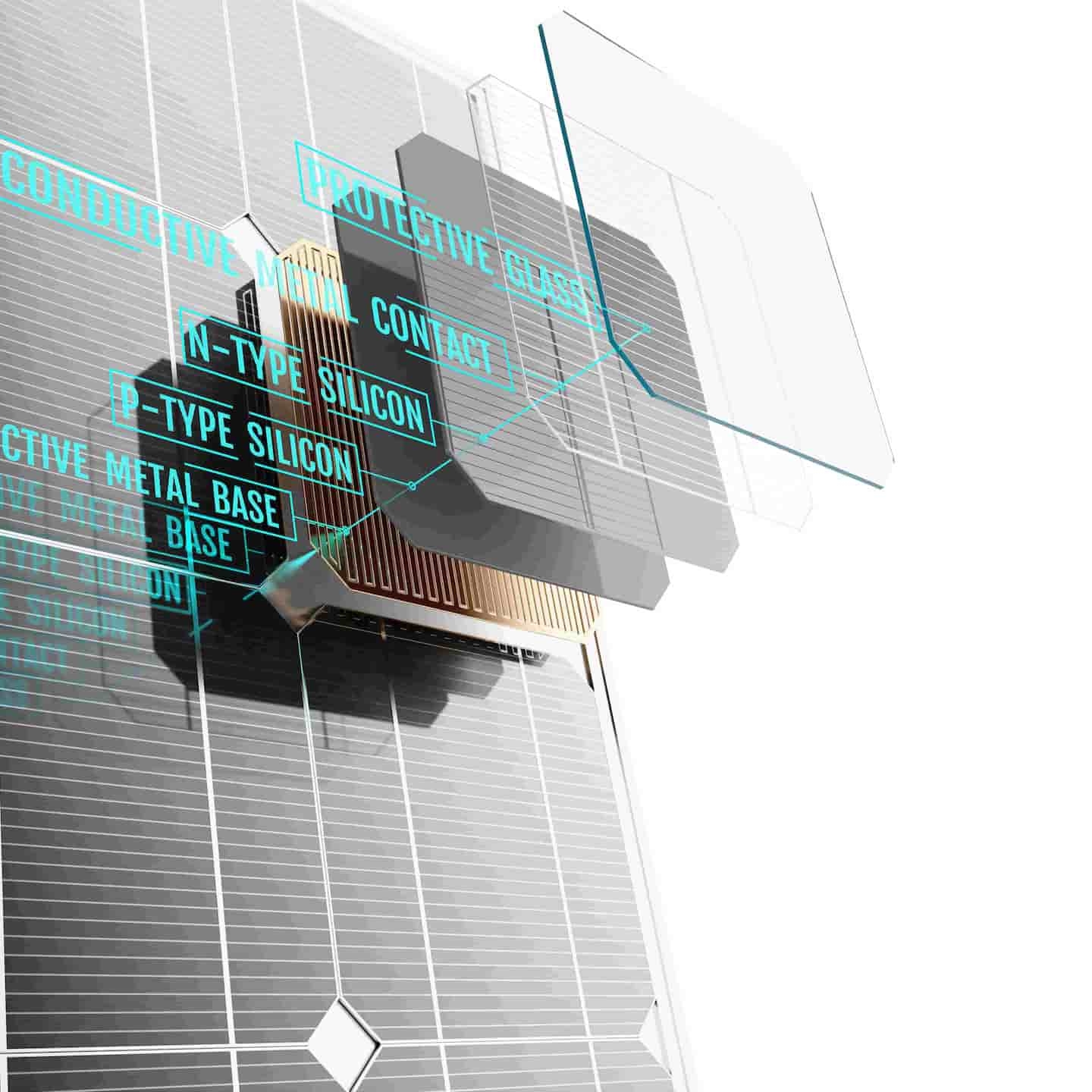.jpg)
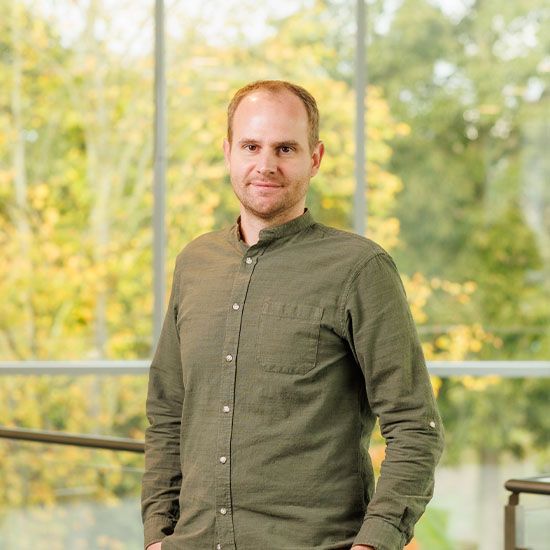
explore more cases.
Demcon multiphysics.
Demcon multiphysics is an engineering agency with high-end expertise in the area of heat transfer, fluid dynamics, structural mechanics, acoustics, electromagnetism and nuclear physics. We support clients from a wide variety of market sectors and help them achieve their goals in research and development with deep physical insights.
We combine fundamental physical knowledge from an analytical approach with Computer Aided Engineering (CAE) simulations tools from ANSYS, MATHWORKS, COMSOL, STAR-CCM+ and FLUKA to setup, execute, analyze and evaluate numerical simulations. The use of Computational Fluid Dynamics (CFD), Finite Element Analysis (FEM / FEA), Lumped Element Modelling (LEM), Computational Electromagnetics (CEM) and Monte Carlo simulations enables us to make a virtual prototype of your design. With these techniques we can simulate the fluid and gas flows, energy exchange, heat and mass transfer, stresses, strains and vibrations in structures and the interaction of electromagnetic fields with other physical aspects like heat generation. Simulation-driven product development increases the development efficiency and reduces the product development time. Our services can therefore fully support you in the designing phase, from idea up to prototype, from prototype to final design.
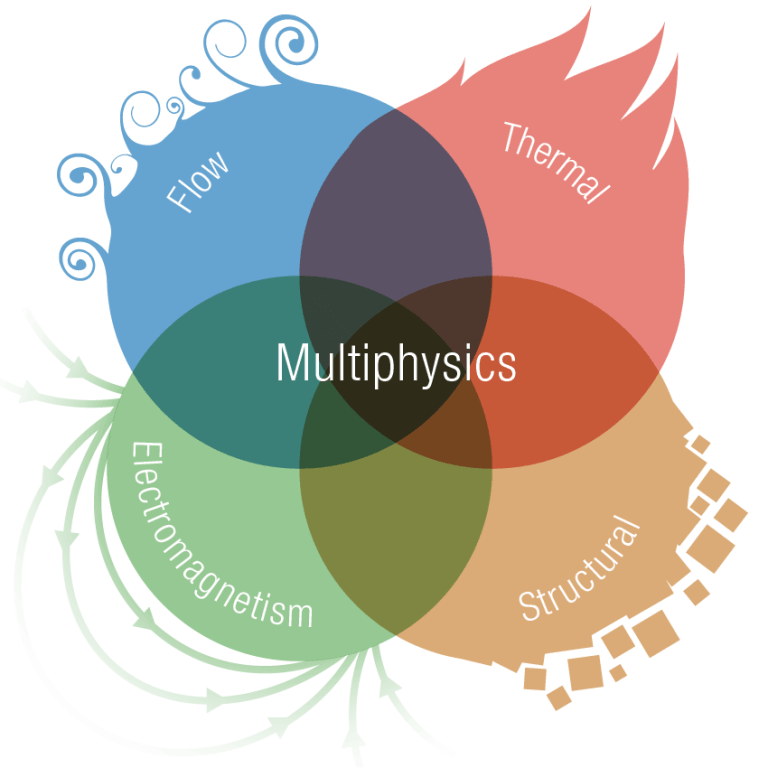