Original
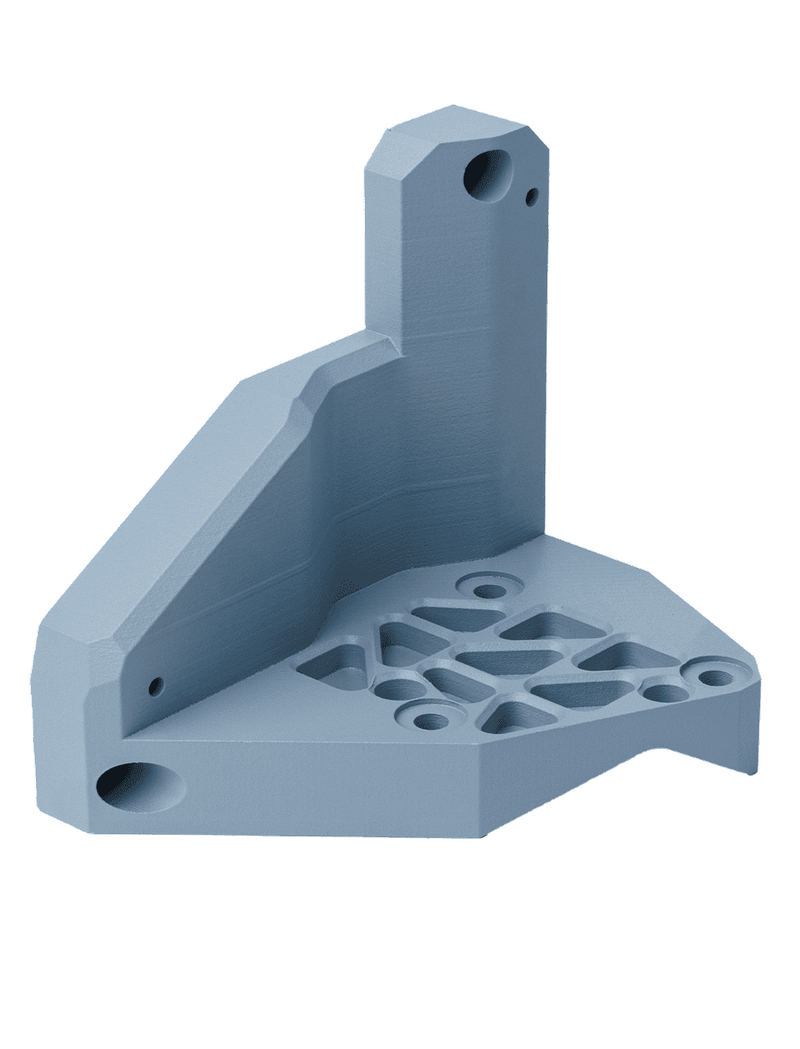
Additive manufacturing opens up the possibility of generating complex shaped parts, allowing almost infinite freedom of design. Such complex shapes do not only make your product looks attractive, but it also offers the possibility of realizing high performance parts. High strength or stiffness of a product can be realized at a relative low weight. However, designing such parts is not straightforward and requires extensive knowledge of engineers. Nowadays, tools have been developed to help engineers in this process. Topology optimization is one helpful tool and is considered as a generative design technique. Although the tool shapes the part for you, the engineer still should make the right choices to get a suitable high-performance part that suits the engineering question.
One stainless steel part for the Extremely Large Telescope (ELT) has been designed using topology optimization during a collaboration between Demcon and K3D. In this design assessment, the question was, “How to make a product lighter, while keeping a certain stiffness?”. The specific part is purposed to fine tune mirror positions for a laser system part of the ELT which searches for extrasolar planets. Its original weight is 4.0kg, which made it highly inconvenient to mount this part and expensive for milling. The result after two design iterations is a more natural shape that could be produced by 3D printing, with a weight of 0.9kg and the ability to sustain its stiffness and strength.
Rapidcenter printed the design in colour to represent the simulations.
The original has a simulation weight of 4 kg
Iteration one has a simulation weight of 1.2 kg
Iteration 2 has a simulation weight of 0.9 kg
A total weight reduction of 77.5%
A lower limit was specified for the stiffness of the bracket together with an available space for the part. Connection points were defined, and the part was then optimized using topology optimization considering 4 different loads. The first design iteration resulted into a part where its stiffness was optimized for a given mass of 1.2kg, so a weight reduction of 2.8kg.
The second design iteration was performed including extensive knowledge of K3D about the printing process. It was investigated how the part can be printed more efficient without printing supports and allowing tinniest features of 0.3mm within the design to get the highest performance. These constraints were included in the topology optimization solver and resulted into a final part of 0.9kg, i.e., an additional mass reduction of 0.3kg or 25%. Moreover, the new design without printing supports resulted into 50% reduction of the material required for printing. In this way a cost reduction of 40% for printing the part between the first and second design iteration was realized during a fruitful collaboration between Demcon and K3D. A clear example of how we can optimize your part in costs and performance.
Demcon multiphysics is an engineering agency with high-end expertise in the area of heat transfer, fluid dynamics, structural mechanics, acoustics, electromagnetism and nuclear physics. We support clients from a wide variety of market sectors and help them achieve their goals in research and development with deep physical insights.
We combine fundamental physical knowledge from an analytical approach with Computer Aided Engineering (CAE) simulations tools from ANSYS, MATHWORKS, COMSOL, STAR-CCM+ and FLUKA to setup, execute, analyze and evaluate numerical simulations. The use of Computational Fluid Dynamics (CFD), Finite Element Analysis (FEM / FEA), Lumped Element Modelling (LEM), Computational Electromagnetics (CEM) and Monte Carlo simulations enables us to make a virtual prototype of your design. With these techniques we can simulate the fluid and gas flows, energy exchange, heat and mass transfer, stresses, strains and vibrations in structures and the interaction of electromagnetic fields with other physical aspects like heat generation. Simulation-driven product development increases the development efficiency and reduces the product development time. Our services can therefore fully support you in the designing phase, from idea up to prototype, from prototype to final design.