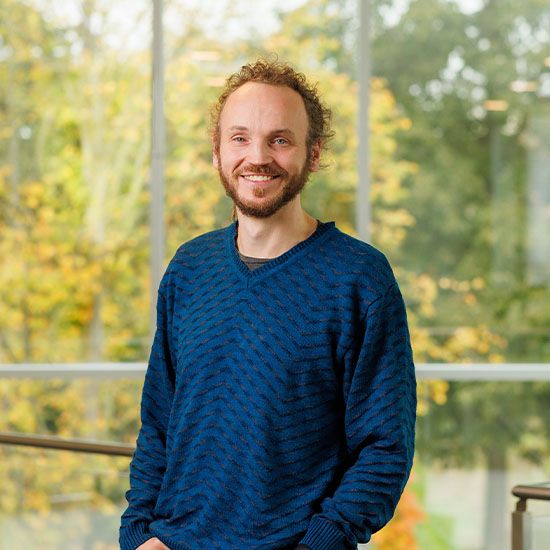
powering batteries efficiently.
The charging mechanism of the battery is based on two coils: a receiver (Rx) and a transmitter (Tx) coil. The Rx coil is embedded in the electrical circuit of the implant, and the Tx coil is positioned inside the external charger. COMSOL Multiphysics was used to design and optimize both coils. The objective was to ensure that enough current is generated in the Rx coil to charge the implant, while minimizing the power losses in the Rx and Tx coils and circuits. The energy that is dissipated in the surrounding skin tissue was one of the limiting design constrains.
In the COMSOL model, the Rx coil was placed 3 cm below the transmitter. The centers of the Rx and Tx coils were displaced with respect to each other by 3 cm, to mimic the real-life situation. The electrical circuit of the implant was simulated with LTspice, and experimentally verified using a breadboard.
Finally, simulations of local heating of the implant and the surrounding tissue were performed for several skin depths of the implant. For these simulations, it was needed to make a coupled EM-thermal simulation using COMSOL.

Wireless power transfer is a very interesting and still developing field, in which electromagnetic physical phenomena are tightly coupled to electronic circuitry. There are many different variations of e.g. antennas, resonant couplings, and coil designs that contribute to a good design. What makes it interesting as a multiphysics engineer is that they are also possible to simulate! With the many disciplines and physics coming together, it makes for big and fun playground where the challenge is finding the right balance between power and power efficiency.
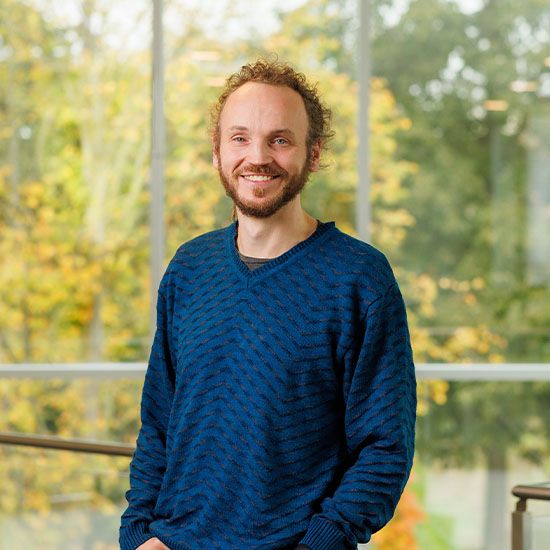
Herausforderungen, die wir meistern.
Demcon multiphysics.
Demcon multiphysics is an engineering agency with high-end expertise in the area of heat transfer, fluid dynamics, structural mechanics, acoustics, electromagnetism and nuclear physics. We support clients from a wide variety of market sectors and help them achieve their goals in research and development with deep physical insights.
We combine fundamental physical knowledge from an analytical approach with Computer Aided Engineering (CAE) simulations tools from ANSYS, MATHWORKS, COMSOL, STAR-CCM+ and FLUKA to setup, execute, analyze and evaluate numerical simulations. The use of Computational Fluid Dynamics (CFD), Finite Element Analysis (FEM / FEA), Lumped Element Modelling (LEM), Computational Electromagnetics (CEM) and Monte Carlo simulations enables us to make a virtual prototype of your design. With these techniques we can simulate the fluid and gas flows, energy exchange, heat and mass transfer, stresses, strains and vibrations in structures and the interaction of electromagnetic fields with other physical aspects like heat generation. Simulation-driven product development increases the development efficiency and reduces the product development time. Our services can therefore fully support you in the designing phase, from idea up to prototype, from prototype to final design.
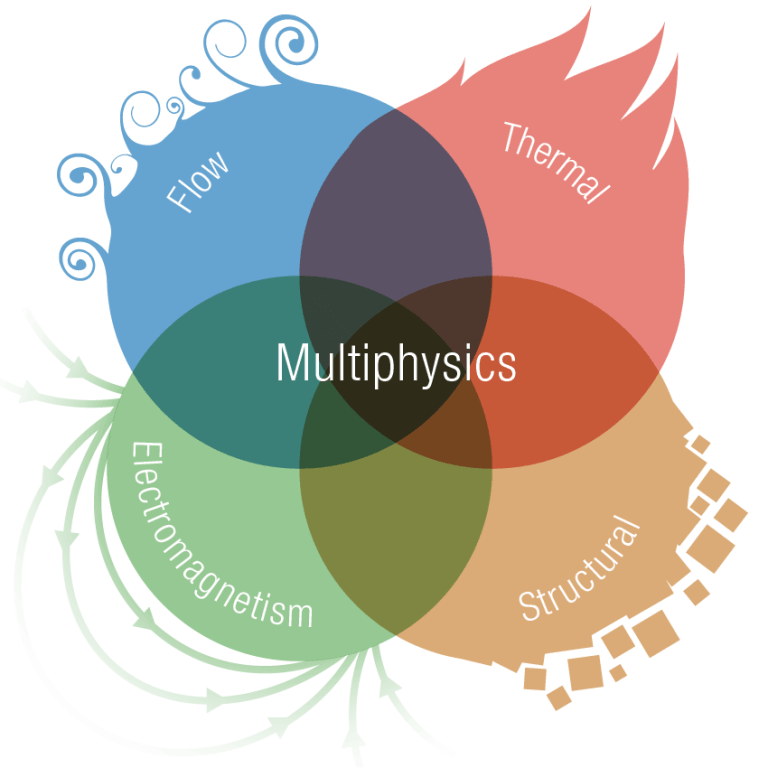