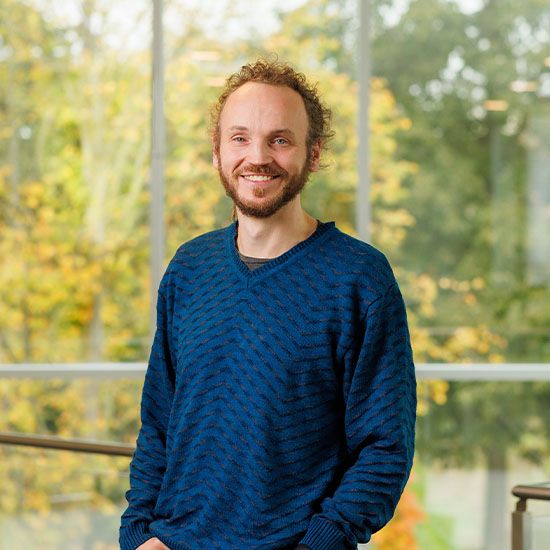
high-fluence irradiation.
1. Firstly, we simulated the radiation damage in depth, using Monte Carlo FLUKA simulations. These provide us with heat load and damage metrics.
2. Secondly, we coupled these results to a 3D COMSOL model. This allows us to determine stresses in detail, and gives us the ability to assess the failure probability of a part.
Using this multiphysics coupling, and some rudimentary assumptions and calculations, we showed that the part is likely to withstand the harsh radiation environment.
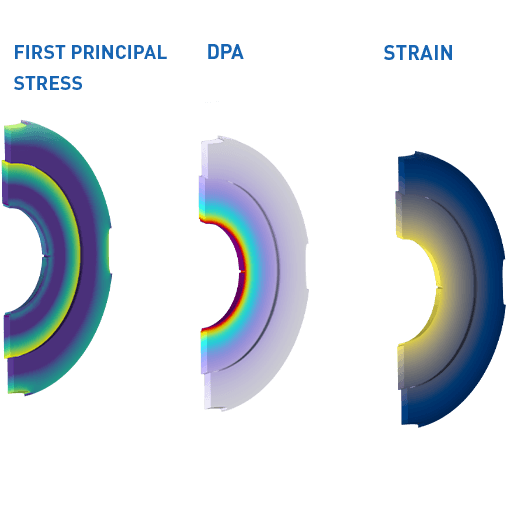
"multiscale, multiphysics"
Unsurprisingly, we often find that coupling physics across multiple domains can be beneficial. In this case, it involves the domains of high-energy particle physics and mechanical-structural effects. Naturally, this multiphysics approach requires expertise in both subdomains. Additionally, the distinct mechanisms involved in these physics domains necessitate the use of different tools, such as Monte-Carlo methods and FEM. By combining these techniques, we were able to predict the effects of irradiation on mechanical-structural properties. Ultimately, this allows us to form a clear understanding of how irradiation impacts various aspects, including structural integrity, performance, and safety.
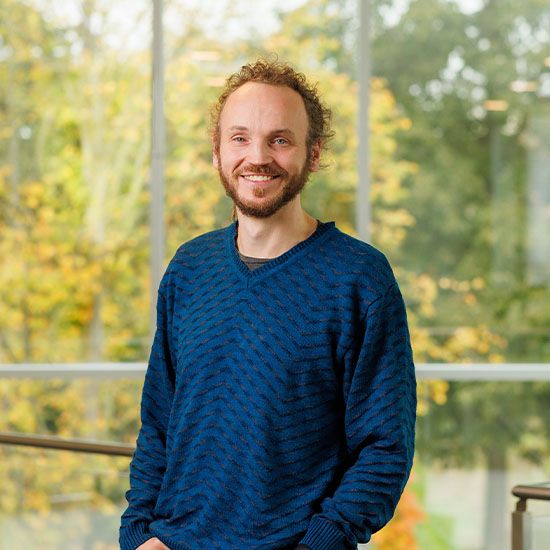
Herausforderungen, die wir meistern.
Demcon multiphysics.
Demcon multiphysics is an engineering agency with high-end expertise in the area of heat transfer, fluid dynamics, structural mechanics, acoustics, electromagnetism and nuclear physics. We support clients from a wide variety of market sectors and help them achieve their goals in research and development with deep physical insights.
We combine fundamental physical knowledge from an analytical approach with Computer Aided Engineering (CAE) simulations tools from ANSYS, MATHWORKS, COMSOL, STAR-CCM+ and FLUKA to setup, execute, analyze and evaluate numerical simulations. The use of Computational Fluid Dynamics (CFD), Finite Element Analysis (FEM / FEA), Lumped Element Modelling (LEM), Computational Electromagnetics (CEM) and Monte Carlo simulations enables us to make a virtual prototype of your design. With these techniques we can simulate the fluid and gas flows, energy exchange, heat and mass transfer, stresses, strains and vibrations in structures and the interaction of electromagnetic fields with other physical aspects like heat generation. Simulation-driven product development increases the development efficiency and reduces the product development time. Our services can therefore fully support you in the designing phase, from idea up to prototype, from prototype to final design.
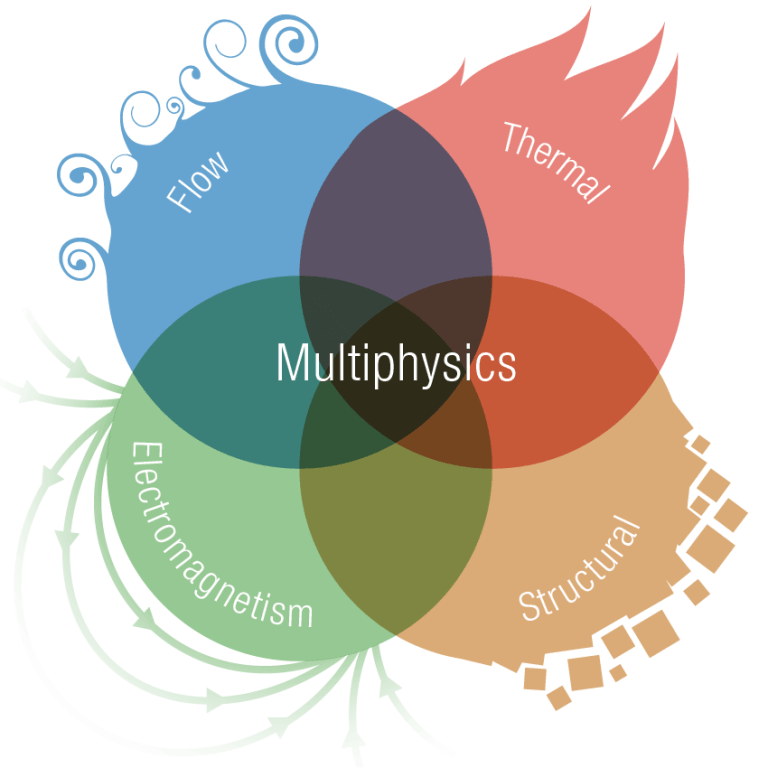