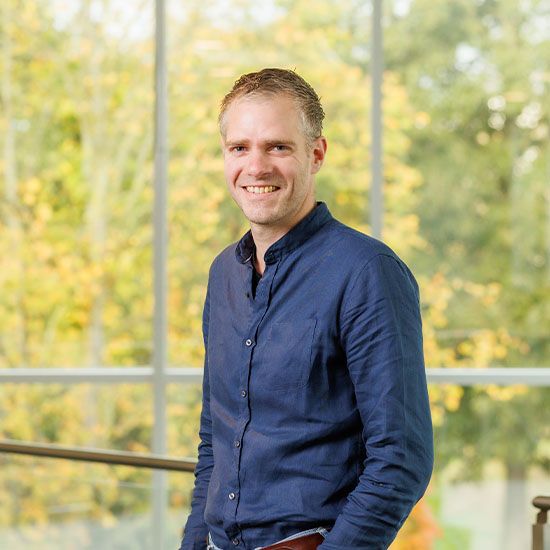
reducing noise problems.
Experts from the area of acoustics and flow visited the engineering and production site of HITEC in the Netherlands to assess the issue and discuss potential solutions with the responsible product owner from HITEC. The available 1/3 octave band sound power level measurement data was reviewed and a running unit was investigated in the workshop. After extensive review, it was decided that the most cost effective and lowest technical risk solution for this case was to design a custom low frequency silencer specifically designed to reduce the tonal noise.
The first step in the design of the custom silencer was to collect a more detailed acoustic signature. Therefore, an independent measurement was conducted. Using an advanced sound intensity probe, the required narrow band source power spectra was obtained. Based on the acoustic signature, one of the acoustic specialists designed the silencer. The silencer’s working principle is based on cavity resonators separated by an acoustic liner based on micro-perforated panels. The Sullivan-Crocker model for cavity resonators was used to find the optimal configuration within the spatial constraints. The final design was verified using an acoustic Finite Element Method simulation.

The team also recognized the importance of the silencer on flow resistance by mounting the silencers on the inlet and outlet of the flywheel module. This was important as the flywheel is continuously running in air at atmospheric pressure, which generates windage losses and causes the release/production of heat. To ensure that the flywheel does not overheat and that good ventilation is maintained, a CFD analysis of the air flow in the flywheel system was made. Moreover, this allowed verification of the pressure levels at the bearings to ensure that no oil is extracted from the bearing due to a local under pressure. The CFD analysis confirmed that the temperature of the flywheel would still be within the specifications after installation of the custom silencer. The better-guided flow actually improved the cooling capacity of the system.
The next step in the development was to complete the mechanical design and to prepare technical procurement documentation. A number of specific mechanical requirements had to be implemented during this step as well. The silencers should be easy to mount and drilling additional holes in the flywheel housing was to be avoided. Moreover, an exchangeable filter was installed to protect the acoustic materials from dirt and dust.
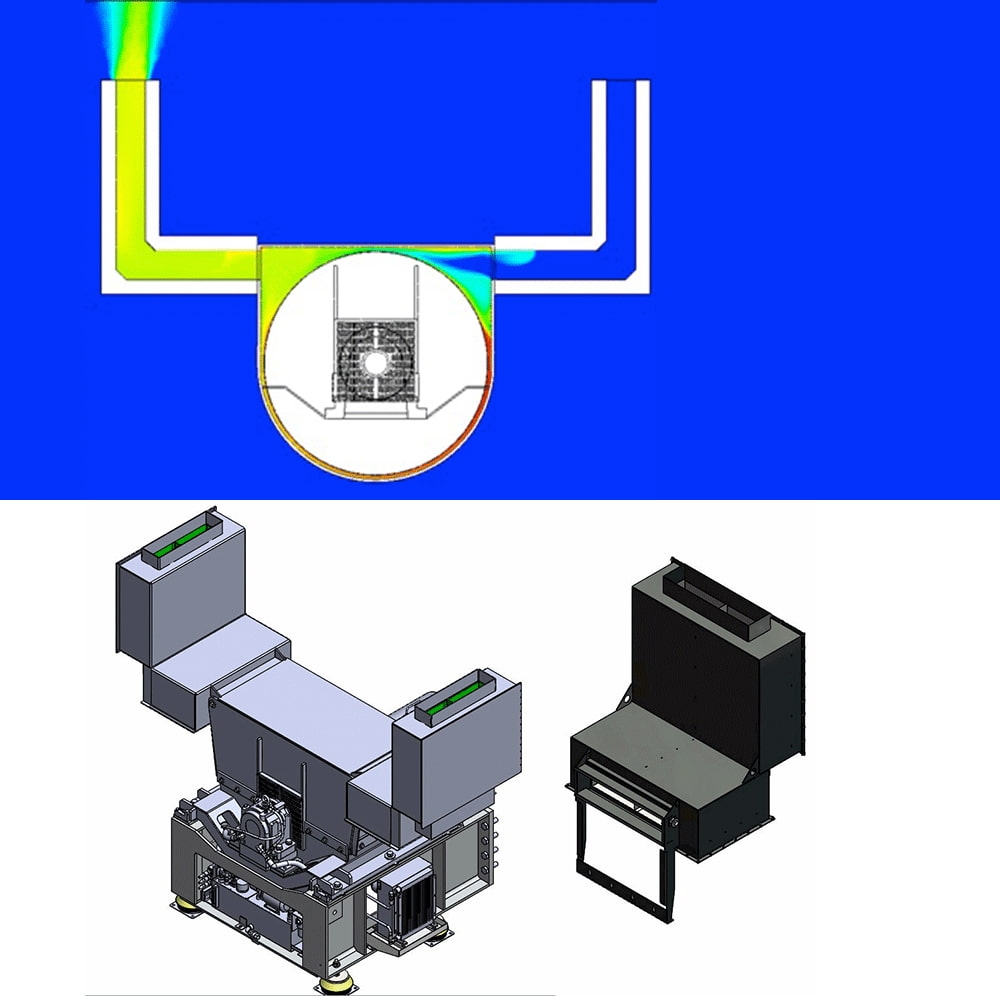
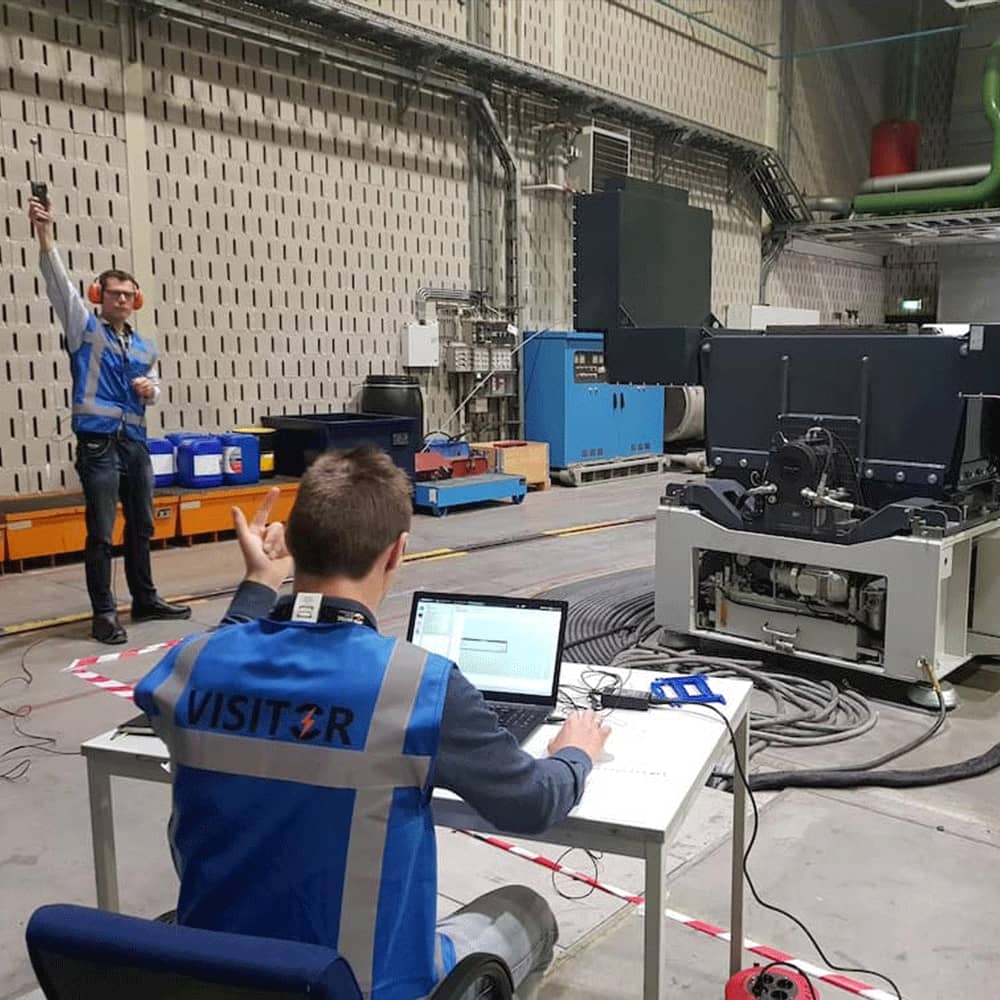
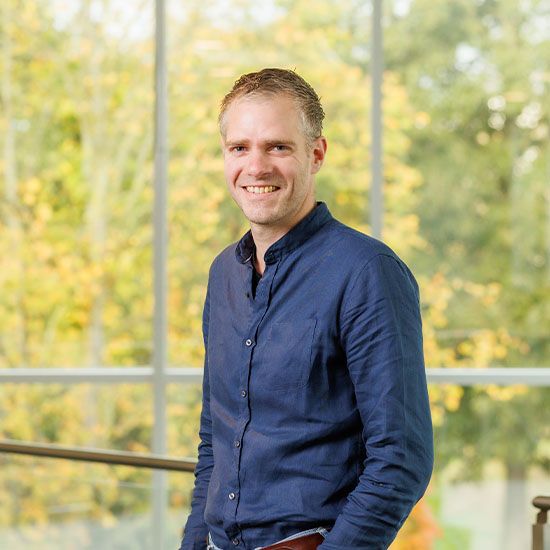
de uitdagingen die wij aangaan.
Demcon multiphysics.
Demcon multiphysics is an engineering agency with high-end expertise in the area of heat transfer, fluid dynamics, structural mechanics, acoustics, electromagnetism and nuclear physics. We support clients from a wide variety of market sectors and help them achieve their goals in research and development with deep physical insights.
We combine fundamental physical knowledge from an analytical approach with Computer Aided Engineering (CAE) simulations tools from ANSYS, MATHWORKS, COMSOL, STAR-CCM+ and FLUKA to setup, execute, analyze and evaluate numerical simulations. The use of Computational Fluid Dynamics (CFD), Finite Element Analysis (FEM / FEA), Lumped Element Modelling (LEM), Computational Electromagnetics (CEM) and Monte Carlo simulations enables us to make a virtual prototype of your design. With these techniques we can simulate the fluid and gas flows, energy exchange, heat and mass transfer, stresses, strains and vibrations in structures and the interaction of electromagnetic fields with other physical aspects like heat generation. Simulation-driven product development increases the development efficiency and reduces the product development time. Our services can therefore fully support you in the designing phase, from idea up to prototype, from prototype to final design.
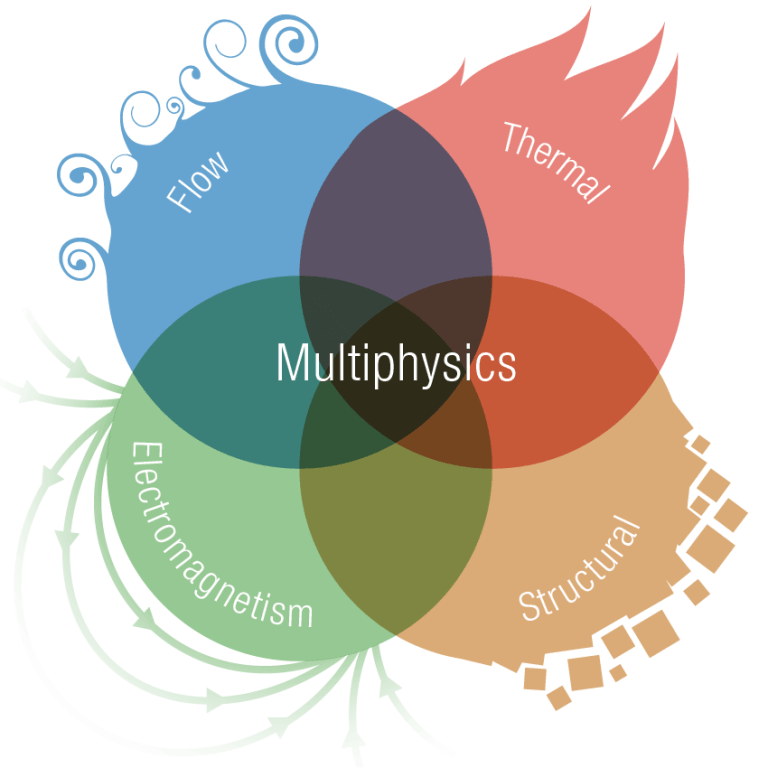