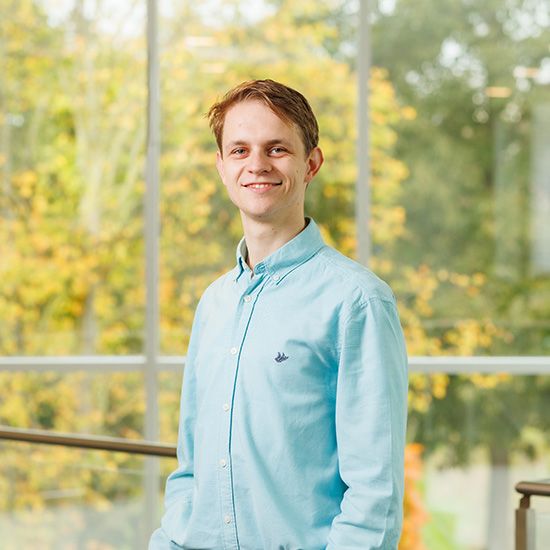
porous materials.
A fast modular set up is designed to experimentally measure the pressure loss through a porous medium. From the data of the experiment, a pressure drop relation dependent on the superficial flow velocity and length scale is extracted.
The results of the experiment are compared with analytical results, comparing Darcy’s law and the Ergun equation, and full detailed simulations, simulating the porous media to its full extend with similar void fraction and permeability.
During simulation, the pressure relation, as extracted from the experiment, replaces the geometry of the porous medium. This new ‘black box’ which simulates the behavior of the porous medium can now substitute the detailed porous media on a system level, making the simulation much faster, and applicable to use on a system level.
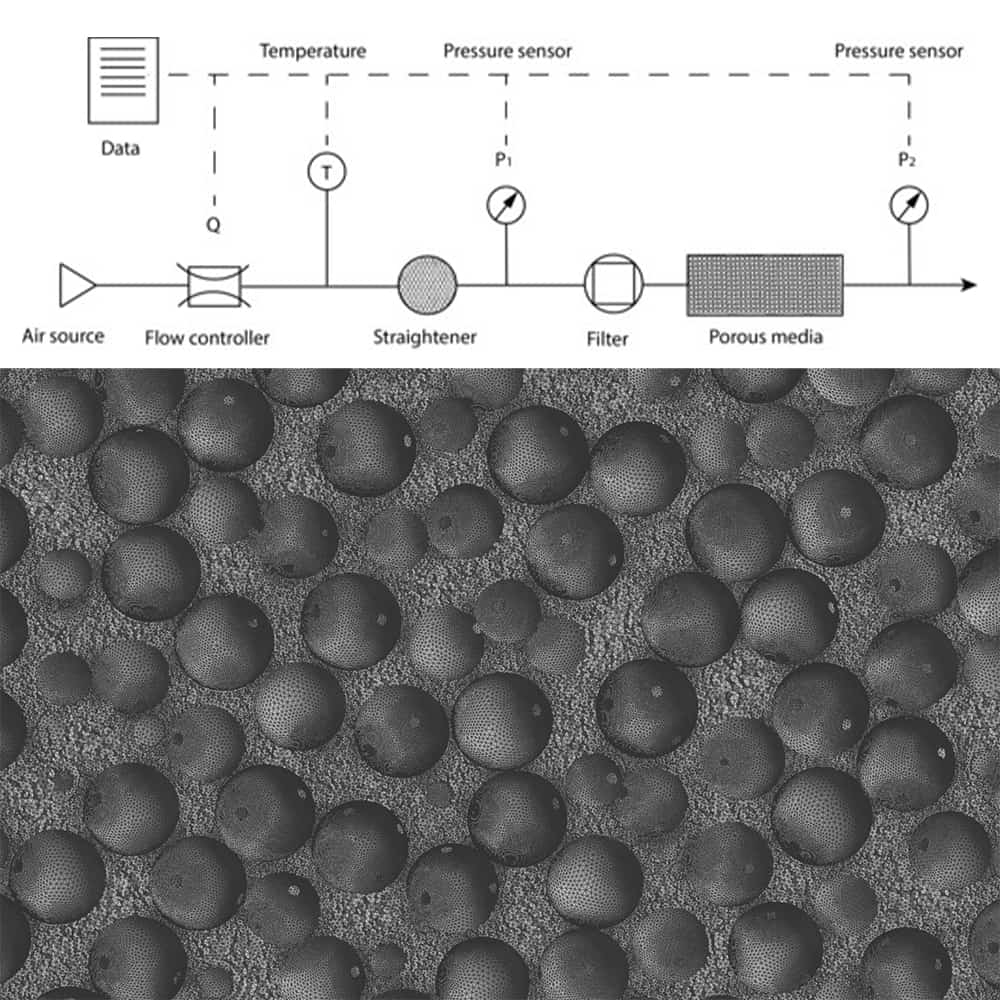
"multiphysics for engineering purposes"
The power of approaching a multiphysics problem lies within correctly including relevant physics and excluding any redundant information on the system. Do I need to take the heat transfer into account or are they negligible? Do I need a simulation or is a hand calculation sufficiently accurate? This approach helps gaining useful information about a system, in little time as possible.
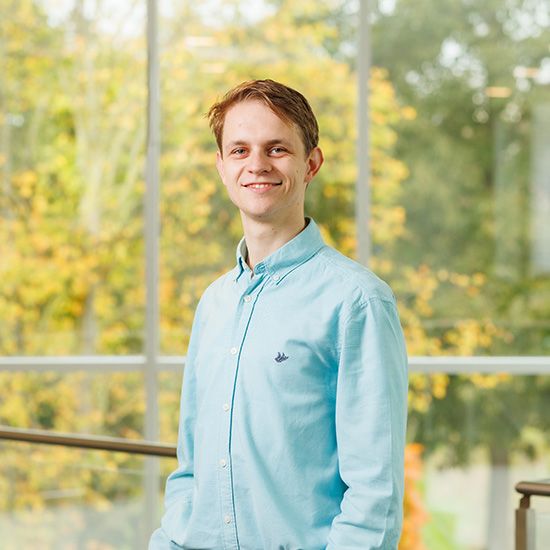
explore more cases.
Demcon multiphysics.
Demcon multiphysics is an engineering agency with high-end expertise in the area of heat transfer, fluid dynamics, structural mechanics, acoustics, electromagnetism and nuclear physics. We support clients from a wide variety of market sectors and help them achieve their goals in research and development with deep physical insights.
We combine fundamental physical knowledge from an analytical approach with Computer Aided Engineering (CAE) simulations tools from ANSYS, MATHWORKS, COMSOL, STAR-CCM+ and FLUKA to setup, execute, analyze and evaluate numerical simulations. The use of Computational Fluid Dynamics (CFD), Finite Element Analysis (FEM / FEA), Lumped Element Modelling (LEM), Computational Electromagnetics (CEM) and Monte Carlo simulations enables us to make a virtual prototype of your design. With these techniques we can simulate the fluid and gas flows, energy exchange, heat and mass transfer, stresses, strains and vibrations in structures and the interaction of electromagnetic fields with other physical aspects like heat generation. Simulation-driven product development increases the development efficiency and reduces the product development time. Our services can therefore fully support you in the designing phase, from idea up to prototype, from prototype to final design.
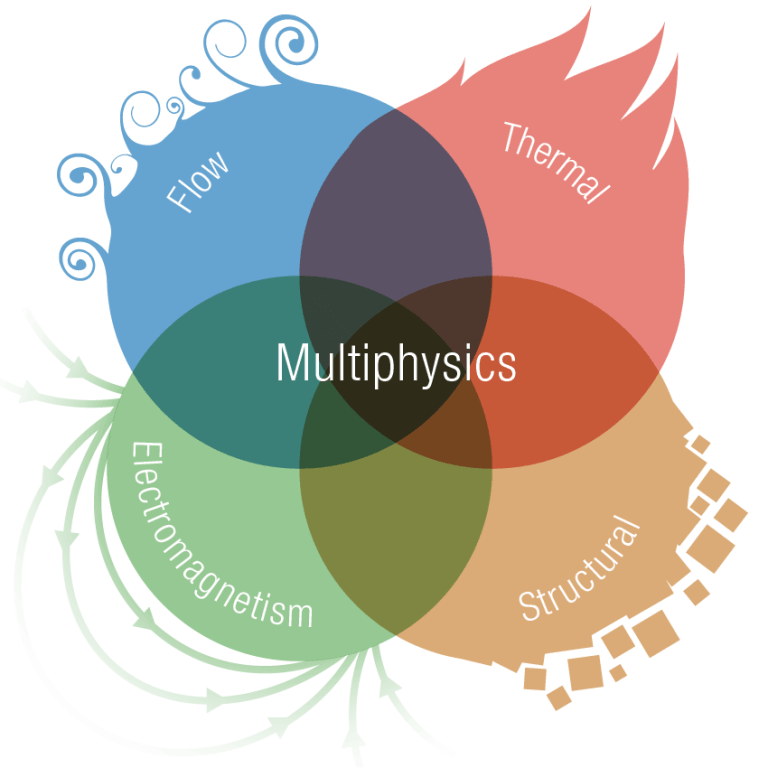